The last mile race: challenging urban logistics
Our Urban Logistics Research Report is out now.
6 minutes to read
From big sheds to small spaces, new industrial development on Australia's east coast is at its highest level since 2007. At the same time, as more businesses embrace the last mile as a key differentiator, there is an increased focus on urban locations as part of the logistics network.
Looking to the future, it’s likely that we will see increased rates of existing infill sites being re-purposed for last-mile use. In this new report, we look at the drivers behind this and discuss the opportunities for the Industrial Logistics sector.
Developers on the front foot to quickly scale up as demand for last-mile rises
As businesses expand their e-commerce capabilities, their warehouse and logistics requirements are growing and evolving, creating a huge opportunity for the industrial sector as a provider of real estate.
In fact, the surge in e-commerce/retail, transport, logistics and manufacturing demand during the pandemic pushed new development completions to a historic 13-year high in 2020.
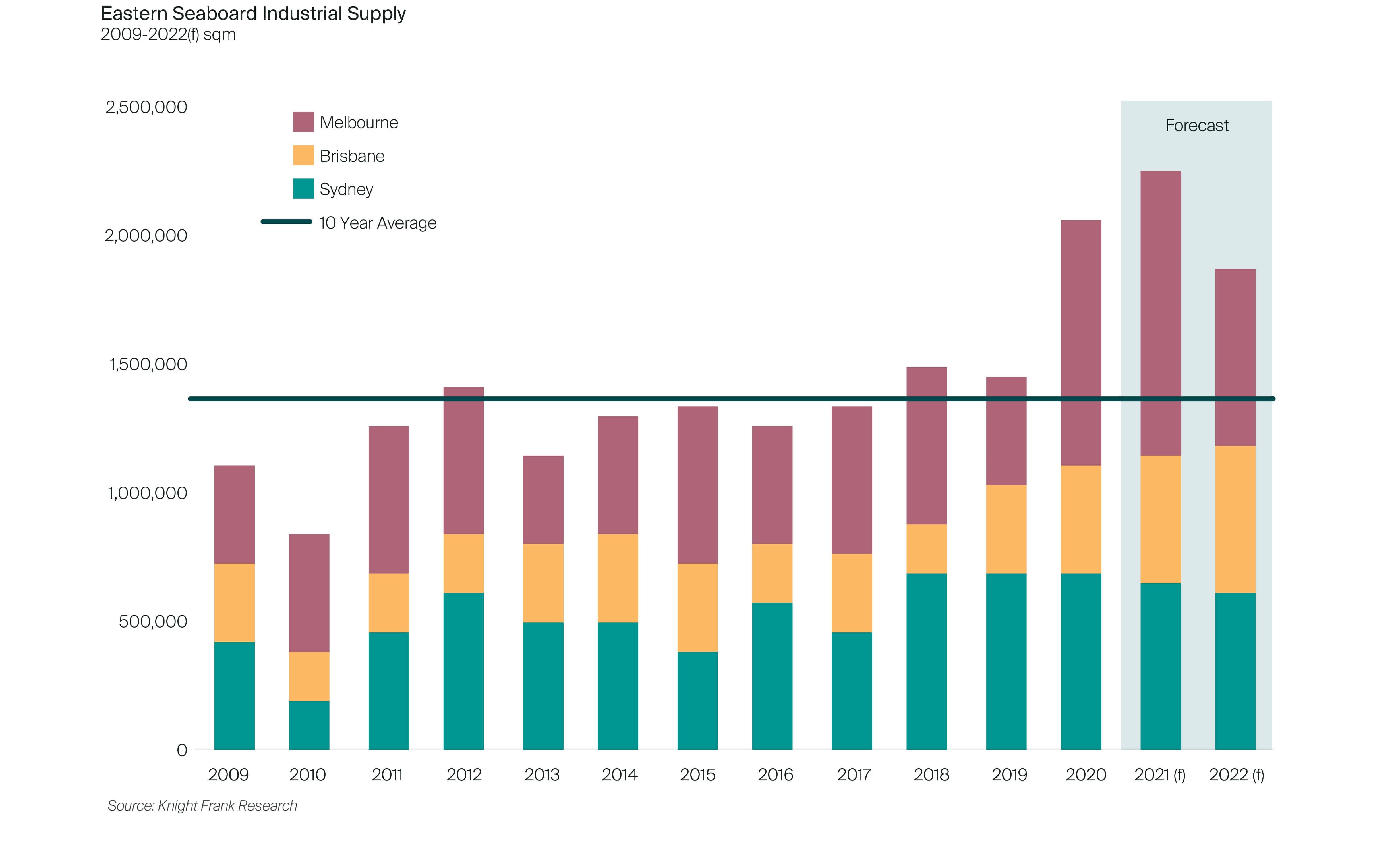
More businesses are competing to invest in tech solutions, increase volumes and expedite delivery to the end-user. This expansion is putting pressure on distribution networks to implement greater efficiencies. It has also underpinned growth in the sector to the point that traditional distribution networks and development facilities that the market has seen on the outer edges of Sydney and Melbourne will not be enough to meet these capacity pressures. Last-mile facilities are also needed to help mitigate these pressures.
The rapid growth of land values in infill locations relative to the outer areas in Sydney and Melbourne demonstrates the shift in this demand as more retailers and distributors seek to store their inventory as close to the end-user as possible in a bid to speed up that last-mile.
However, the increased cost of these infill locations where land is limited is resulting in increased use of automation and generating new demand for building conversions, compact building designs, multi-level warehousing and alternative last-mile delivery solutions to maximise the capacity of available smaller footprints.
Option to convert underutilised assets
The re-use of existing supply chain or building infrastructure already in place in some urban areas may make them good candidates for certain industrial and logistics activities, increasing the scope for owners/developers looking to capitalise on the rise in demand.
The tightly held nature of urban locations is fuelling the appetite to acquire existing infill sites that can be re-purposed for lighter industrial use, mini-store or last-mile.
Retail, parking spaces and light industrial to logistics conversions have been taking place across Europe and the UK, foreshadowing similar opportunities for Australian markets. In one recent example, the City of London leased 39 car parking spaces to Amazon for a last-mile logistics hub that will use e-cargo bikes for delivery.
In Australia, the first signs of this trend were seen in 2019 when Dexus bought Homemaker Prospect, in Sydney’s west, announcing plans to convert it into an industrial property within five years. Last year, two separate sites in South Sydney sold to Goodman Group and Charter Hall for their future infill redevelopment potential, 70-80 Euston Road (6,633 sqm) and 520-530 Gardeners Road (19,000 sqm). Charter Hall has already earmarked the Gardeners Road site for the development of a last-mile multi-storey warehouse facility.
Need for speed driving greater adoption of automation
Linked to this, improvements to technology have enabled operators to make better use of space, expanding the opportunities to occupy smaller footprints in urban areas where land is priced at a premium. This could present opportunity to other sectors where the space is underutilised, be it retail or secondary industrial, by converting or redeveloping the unit as a micro-fulfilment centre or a standalone dispatch or click-and-collect centre. For example, this type of facility could then be let to a 3PL to service the dispatch, delivery and returns of customer orders. A landlord could offer a lower or subsidised rent than its original retail use, helping to fill the vacant space and support occupancy rates.
Opting for a pure ‘dark store’, which is used only for fulfilment could also create opportunity for existing underutilised or redundant assets in urban fringe locations. This type of shift could put some pressure on planners to allow conversion to industrial use in certain urban locations and potentially see industrial rents repriced in those urban fringe locations.
Grocery giants lead, but others will follow
Coles and Woolworths have reported massive growth in their online sales and ramped up their plans for automation in their warehouses as they double down on their e-commerce strategies to deliver online orders faster while competing for market share. As a result, both retailers have been actively scaling up their warehouse and distribution centres, committing to lease more than 350,000 sqm in new distribution centres to be built in Sydney, Melbourne and Brisbane between 2020 and 2024.
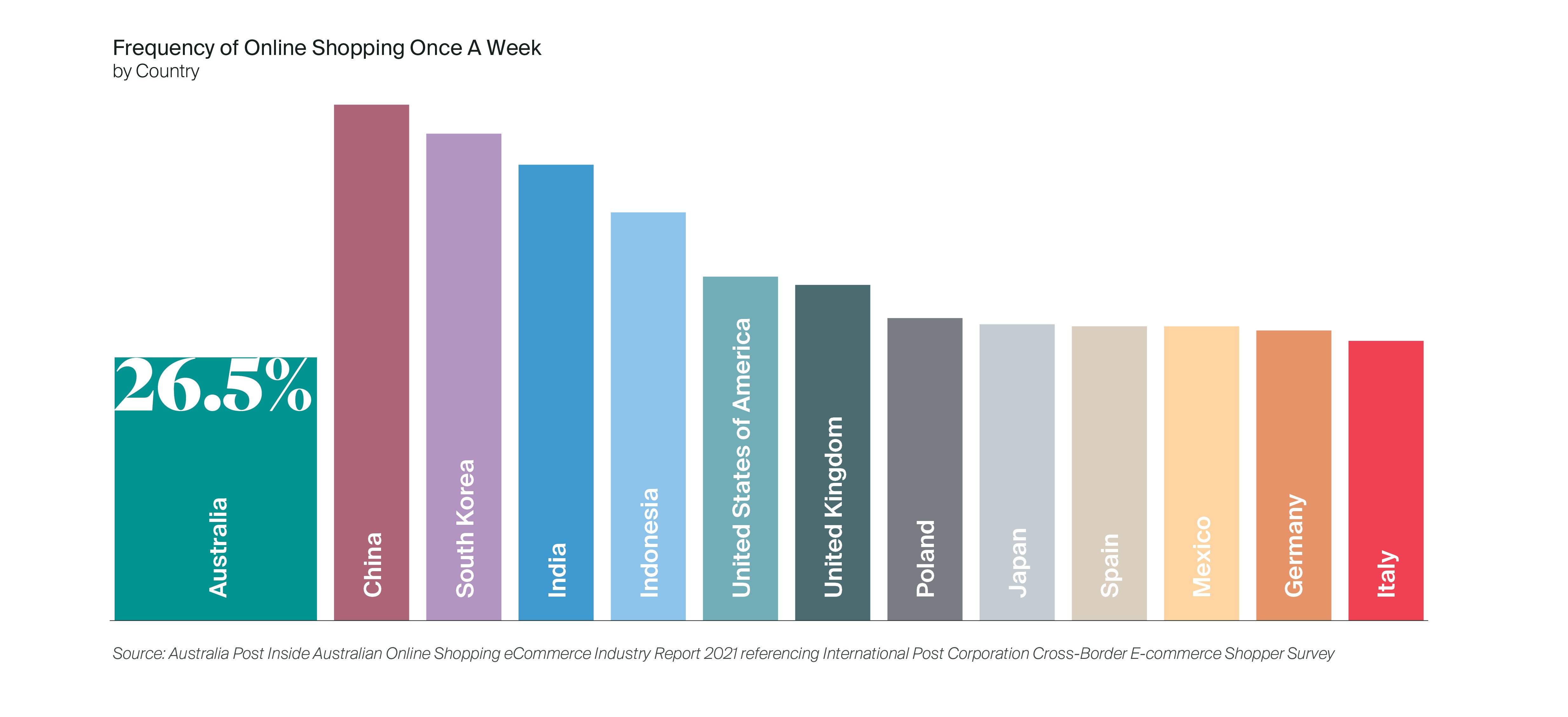
Although the push towards automation has been most evident with the grocery giants, other businesses are exploring ways to bypass traditional distribution models, and this is prompting a significant shift in the industrial warehousing market from a widening range of users.
Jaycar Electronics Group (Jaycar), which is relocating from their Rydalmere facility Sydney’s inner north west to Eastern Creek, in Sydney’s outer west into a 21,995 sqm purpose-built automated warehouse and distribution centre, said “the move positions the group to leverage growth in online retail by enabling the lowest possible cost to fulfil customer requests in an increasingly competitive space.” In another example, AS Colour, a manufacturer of premium apparel pre-committed to lease an 18,110 sqm purpose-built automated logistics facility in Truganina, Melbourne as it wanted to find a way to pick orders faster with minimal handling.
Automation does require operators or developers to invest more in their facilities, but these costs will come down over time. Eventually there will be a greater widespread adoption of automation, even at low levels in the design of the building or fitout.
It's not one model fits all
The last mile has become a critical aspect of the supply chain. Advancements in technology and need for more sophisticated supply-chain networks, in conjunction with the change in the intensity of both customer and business demand, are driving changes to the industrial landscape globally.
This is intensifying the pressure on order fulfilment, as well as traditional outbound supply-chain facilities, and increasingly reverse logistics, which is said to require about 15-20% more floor space than a traditional outbound supply-chain facility.
The industrial market will see more businesses partnering up with tech providers to develop and implement some of these solutions, creating further opportunity as they relocate or expand existing warehousing facilities. Investment in automation solutions will also increase the opportunity to repurpose or re-use underutilised space for last mile.
Given the acceleration of the e-commerce sector post-COVID and the accompanying necessity for further innovation and resilience in supply-chain management and distribution solutions, urban logistics in Australia will remain a prominent sector.
For more information, contact:
Katy Dean
Associate Director, Research & Consulting
Knight Frank Australia
+61 2 9036 6612
Ben Burston
Chief Economist, Partner, Research & Consulting
Knight Frank Australia
+61 2 9036 6756